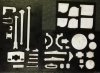
Although I enjoy the use of CAD tools to design my models I do have to use numerous old fashioned processes to make them. One of the most dated and quite traditional machining processes is to use a pantograph milling machine, in my case to make a number of blanks. Some of you have invested in CNC desktop and/or laser cutting devices, which look quite appealing every time I undertake these tasks...
Some of the details of this quite laborious yet still time saving technique are outlined a bit.
I print paper templates out at a predetermined scale of either 3:1 or 5:1, then stick them to plastikard sheet (1.5mm thick and upwards) using solvent. These are then fretted out and filed or smoothed to shape. the templates or profiles are stuck to a backing sheet of plastic and then taken down to the pantograph mill.
The sheet metal stock is stuck down with double sided tape onto another sheet of plastikard, leaving a clearance border.
Clamps secure the material to the work tables of the machine and if necessary all the rivet or hole centres are spotted with a centre drill. The cutters I use are disposable 1.5mm 3 flute for most work. Rarely I employ 1mm cutters but these are for small slots such as those in expansion links, or for areas where a tighter radius inside corner is desirable.
I have tried hard to select free machining grades of both brass (CZ121) and nickel silver (NS101 or NS103) where possible as they really do make life easier. Beware trying to use etching grades of these materials, particularly of nickel silver, as these snag and grab at the cutter very easily and leave a poor finish. For thicker n/s I often employ a cutting oil brushed on, and this obviously prolongs tool life and improves cutting finish at the expense of everything being covered in clag.
duplicates are made as required advancing the work table in nice round numbers. Completed parts removed with a modified artists pallete knife (just sharpened the edges a bit to slide under parts more easily)
Once into a routine, the rhythm of making parts makes the time pass quickly!
removing sections of double-sided tape is often required, as is removing cutting fluid residue.
The cylinder covers are the first time I have jigged a part up on my pantograph machine to counterbore a profile, and it turned out I need not have worried. In most cases it just working out how to hold the workpiece. I soldered the blanks, two of which are shown as these are for the front of the cylinders, onto piece of scrap brass bar.
The bogie is up on its wheels, and the compensated axleboxes articulate nicely.
Though I use lots of manual machining methods and skills, and it might seem a bit of a shame to a 'purist' like me, I am actively investigating the new digital additive manufacturing 3D printing techniques and CNC profiling, now that I am satisfied that these processes have reached a sufficient quality to cost ratio...
Best regards
Tom