Nick Dunhill
Western Thunderer
As one job draws to an end, another begins. This time we are returning to the neolithic period to make a GWR no 34 in S7.
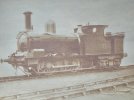
On first inspection the etches seem to be ok, but you can never tell until we begin nailing them together. The client had been very thorough in sourcing all the other parts required, and also supplied drawings.
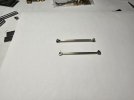
As always I began with the rods. They were supplied by Premier Components, but the client requested that I beef up the bosses with an overlay of thin nickel silver sheet, filed to shape and with an added a brass oil pot bung.
The chassis frames and associated components were dressed up, but new stays had to be cut to convert the chassis to S7.

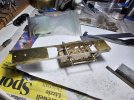
The rear driving axle would run in a fixed top-hat bearing and the front axle in a Slater's cast brass axlebox to add some compensation. It is worth reporting that the centres of the coupling rod and the centres of the etched bearing holes in the frame were a mile out....well around 0.75 mm. This would result in a jammy mechanism if not altered. It didn't matter in this case as we could easily locate the axlebox in the correct location using the rods and some jury axles.
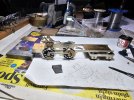
This resulted in a nice free running chassis, which I levelled on a sheet of plate glass, and made the bogie. All runs very nicely, and traverses a 5' 6'' curve with some to spare.
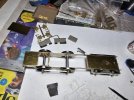
More next week.
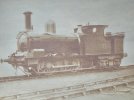
On first inspection the etches seem to be ok, but you can never tell until we begin nailing them together. The client had been very thorough in sourcing all the other parts required, and also supplied drawings.
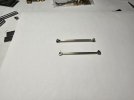
As always I began with the rods. They were supplied by Premier Components, but the client requested that I beef up the bosses with an overlay of thin nickel silver sheet, filed to shape and with an added a brass oil pot bung.
The chassis frames and associated components were dressed up, but new stays had to be cut to convert the chassis to S7.

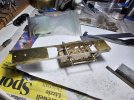
The rear driving axle would run in a fixed top-hat bearing and the front axle in a Slater's cast brass axlebox to add some compensation. It is worth reporting that the centres of the coupling rod and the centres of the etched bearing holes in the frame were a mile out....well around 0.75 mm. This would result in a jammy mechanism if not altered. It didn't matter in this case as we could easily locate the axlebox in the correct location using the rods and some jury axles.
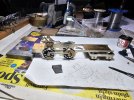
This resulted in a nice free running chassis, which I levelled on a sheet of plate glass, and made the bogie. All runs very nicely, and traverses a 5' 6'' curve with some to spare.
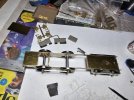
More next week.