Locomodels
Western Thunderer
This is probably going to be a long, tedious and boreing description of how I build crank axles. This is just my method, there are, no doubt, several better ways to go about it. So, as I know many of you build your own axles, if and when my method differs from yours, please let us know. It might help me to build better axles. Even if you have never built one, but think that there are better techniques, let us know your thoughts. One never stops learning.
The very first thing to do, of course, is your research and few things are better than having a works GA drawing available. Which I am fortunate enough to have for this loco. Anyhow GA’s are always wonderful to look at and just enjoy, so definitely worth any costs involved.
OK we have the details, have decided on any compromises necessary and are ready to go.
So to start at the beginning, we cut out the webs. Mine were done on my pantograph mill. Now I know several of you have these beasts so you can skip this bit. For those of you who may not recognise one if you walked into it, here are some pictures. There are several different makes and each make comes in several different sizes. For the record mine is a Taylor-Hobson JH, this is the largest that they made and as you can see it is some 4’6” high, 2’0” wide and about 4’0” deep, so you need quite a lot of space for one and, preferably a reinforced floor, as it is bl**dy heavy. Probably four or five hundredweight. She is getting on a bit now as she is 56 years old, now I know that it is un-gentlemanly to mention a lady’s age, but she is a tough old bird and will certainly see me out.
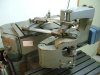
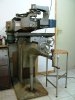