Peter Insole
Western Thunderer
Way back in the early 1970's, a friend of mine started to build a petrol/electric version of an LMS 10000 locomotive in 5 inch gauge. He was inspired by a similar Brush type 4 that a member of the Cambridge Model Engineering society had completed and was operating. I accompanied my friend when he went over to the group's track on a couple of joyous occasions.
On one of those days, a large gentleman arrived in an estate car, bringing with him a partly completed "LBSC Tich". He obviously had also been charged with taking care of his tiny, toddler son! He had a simple solution to the problem of being able to fully engage in the serious business of model engineering - and childcare at the same time...
He produced two contraptions from the back of his car - one rather odd looking motive power unit, and another was a driving truck. The loco had very basic, bare timber, wagon style underframes - and get this... an old, vitreous enamelled bread bin, complete with handles and lid, some wires and a switch hanging out, and the whole shebang screwed on top!
The container was a pale green colour, with the original large legend "Bread", in black serif letters on the side - to which the chap had slightly crudely added above and below "The Flying" and "Bin"!
A motorcycle battery was dropped inside and connected up - then the very small boy was installed on the truck and handed the switch - and he quite happily whizzed off, independently on the circuit! Round and round he went - goodness knows how many times in the next hour or so - but I seem to recall it was until the battery ran out?!
That hilarious vision has left a lasting impression me... and I have been known to refer to it on many occasions since!
Well, after the passage of so many years, I am now convinced the time has finally come where there is a pressing need for our own, albeit marginally more grown-up version of such practical traction!
The key requirements are that it must be cheap, extremely simple, robust enough to suffer all but the worst weather, rough handling, hard knocks and survive being stored in a garden shed!
I think I have found an ideal candidate?
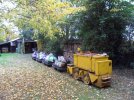
(Copyright image shown here for illustrative purposes only)
We already have a set of wheels, some timber and sheets of 9mm ply, steel angle, a battery and various other electrical bits and bobs in stock... while a 12V motor is on order - so all that was needed was a drawing to work from:
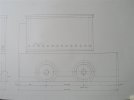
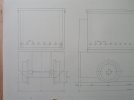
It is not to scale, but more a compromise design, based on practicality, the available wheels, size of battery etc., that I hope will present a "flavour" of the genuine machine?!
I am still severely restricted by the hours that I can use noisy tools in the workshop, but I did manage to get the main frame and headstock blanks shaped yesterday, and hope to do the cut out details and begin assembling them by this evening...?
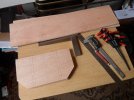
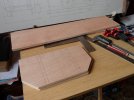
This should hopefully be kept as a bit of a speedy, fun-running flyer of our own!!
Pete.
On one of those days, a large gentleman arrived in an estate car, bringing with him a partly completed "LBSC Tich". He obviously had also been charged with taking care of his tiny, toddler son! He had a simple solution to the problem of being able to fully engage in the serious business of model engineering - and childcare at the same time...
He produced two contraptions from the back of his car - one rather odd looking motive power unit, and another was a driving truck. The loco had very basic, bare timber, wagon style underframes - and get this... an old, vitreous enamelled bread bin, complete with handles and lid, some wires and a switch hanging out, and the whole shebang screwed on top!
The container was a pale green colour, with the original large legend "Bread", in black serif letters on the side - to which the chap had slightly crudely added above and below "The Flying" and "Bin"!
A motorcycle battery was dropped inside and connected up - then the very small boy was installed on the truck and handed the switch - and he quite happily whizzed off, independently on the circuit! Round and round he went - goodness knows how many times in the next hour or so - but I seem to recall it was until the battery ran out?!
That hilarious vision has left a lasting impression me... and I have been known to refer to it on many occasions since!
Well, after the passage of so many years, I am now convinced the time has finally come where there is a pressing need for our own, albeit marginally more grown-up version of such practical traction!
The key requirements are that it must be cheap, extremely simple, robust enough to suffer all but the worst weather, rough handling, hard knocks and survive being stored in a garden shed!
I think I have found an ideal candidate?
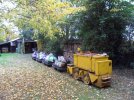
(Copyright image shown here for illustrative purposes only)
We already have a set of wheels, some timber and sheets of 9mm ply, steel angle, a battery and various other electrical bits and bobs in stock... while a 12V motor is on order - so all that was needed was a drawing to work from:
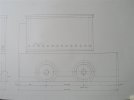
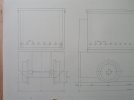
It is not to scale, but more a compromise design, based on practicality, the available wheels, size of battery etc., that I hope will present a "flavour" of the genuine machine?!
I am still severely restricted by the hours that I can use noisy tools in the workshop, but I did manage to get the main frame and headstock blanks shaped yesterday, and hope to do the cut out details and begin assembling them by this evening...?
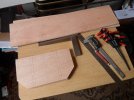
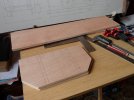
This should hopefully be kept as a bit of a speedy, fun-running flyer of our own!!
Pete.