Dave
Western Thunderer
Evening all,
I have wanted a model of this hefty saddletank since I first saw a photo of it in the Industrial Railway Society Lincolnshire & Rutland handbook and so decided to scratchbuild it.
1814 was built in 1913 for Walter Scott Ltd. who operated a steel works in Hunslet and ironstone quarries in Lincolnshire. It started off as Walter Scott No. 2 and later became Crosby Ironstone No.4 before becoming No.2 in the fleet of United Steels Ore Mining Branch. It was scrapped in 1962.
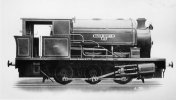
Frames, made from 40 thou. engraving brass, layered with 18 thou. hard brass. Hornby Peckett wheels and axles, bought as spares.
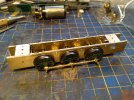
I have wanted a model of this hefty saddletank since I first saw a photo of it in the Industrial Railway Society Lincolnshire & Rutland handbook and so decided to scratchbuild it.
1814 was built in 1913 for Walter Scott Ltd. who operated a steel works in Hunslet and ironstone quarries in Lincolnshire. It started off as Walter Scott No. 2 and later became Crosby Ironstone No.4 before becoming No.2 in the fleet of United Steels Ore Mining Branch. It was scrapped in 1962.
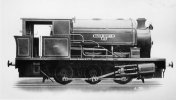
Frames, made from 40 thou. engraving brass, layered with 18 thou. hard brass. Hornby Peckett wheels and axles, bought as spares.
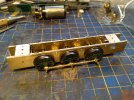