I have got the fine sand ready now for the big bending session, but fancied sorting out the materials for the flange joints first. As it happens, I am down to a small remaining fragment of 4mm brass sheet, perhaps just enough, at a squeeze for the two saddle tank bottom fittings, but no more. I will require another piece for the right hand well tank, while the left hand side has a compression nut attachment. The company that I originally ordered the brass from used to be happy to cut down to minimum sizes required, but unfortunately they have exhausted their own stock now - so I would have to go elsewhere. Unfortunately, I cannot find anyone that sells anything other than standard size sheets - and that at an eye watering price at the moment too! I am not splashing out on a load of extra material that at this late stage of the build, I would be fairly unlikely to find a use for!
It is approaching the point now where there are a two or three features to complete this project that are notably beyond my own ability or facilities to complete without having to call for some outside assistance. I never cease to be amazed by the generosity of friends, but I am always painfully aware of how easy it is to rather enthusiastically promise help, only to find that other life pressures make it impractical or almost impossible to fulfil. While always grateful for any offers, I would prefer not to ask in the first place!
One such issue that has been bothering me for quite a while is the two cylinder lubricators, looking much like brass flower pots with peculiar lids, and prominently perched up front on the running plates and either side of the smokebox.
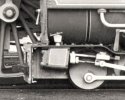
As can be seen in the above images, there were two varieties: The original Horwich pots were more tapered, with a deep lip to accommodate the female threaded section, whereas the later type (being demonstrated by my granddaughter on "Wren") were plain sided and slightly broader. Studying all the photographs to hand reveals that both versions seem to have been distributed amongst the entire class until withdrawal, including evidence that some engines carried one of each at the same time.
One problem for me is that the lubricator only has a single point of attachment, being threaded through a hole in the running plate and into the top of the cylinder... and of course, that part of the latter is made of MDF. While there should be enough meat for a screw to bite into, the lid has that "bench vice" type sliding handle... so if the pot is simply turned out of a solid brass lump, (as it only needs to be for the sake of appearance) I reckon with such leverage available to inquisitive fingers, it wouldn't be too long before the entire body works loose!
Besides that particular concern, I would
really rather like the lid to be removable anyway, thus revealing the internal workings, complete with some nice, gooey looking, but solid imitation of steam oil within!
Entirely for educational purposes... naturally!
Returning however to the immediate task; I wondered if the serious brass shortage, plus a desire for a 10mm pipe compression fitting might be satisfied at my local B&Q? Admittedly, their prices are a bit steep for everything, but then again, I do enjoy the convenience of a very handy discount card
and an equally useful bus-pass to offset much of the penalty!
Picking a sunny day last week, I hopped on a bus, and shortly arrived thereafter to peruse amongst the company's finest brassware products in the plumbing aisle. I was mainly searching for some sort of flange/bracket or cap nut that could cut up and adapted for the "Equilibrium" (official Horwich terminology!) balance pipe fitting.
I found something, and then had one of those "Here, hang on a minute" moments:
A 3/4 inch, female threaded, (weirdly labelled as 1/2 inch?) exterior wall, tap fitting not only provided a neat little baseplate... but the tap socket looked pretty much spot-on size wise for one of those lubricators!
Win, win wahoo!!
I came out with two tap fittings, a pair of blanking caps, and even the hoped for 10mm pipe jobbie, then after a producing quick trace from the G.A's when I got home, set to with the hacksaw...
The brackets (above right) will, after chopping off the third arm and some subsequent fettling, do the twin studded pipe ends quite nicely, whilst the internal bore of the main body turns out to be perfect for our purposes at 12mm!
When scaled down, the hexagonal base of the lubricator also comes out as 12mm, so I was able to round off short sections of pre drilled and tapped 12mm hex in the drill press to form a tight, push fit, solder up solidly and then back in the press to dress down to the final shape with flat and rat tail needle files:
From the outside, the soldered joint between the two parts is well hidden in the coning under the pot bowl, and just at the upper root of the waisted section.
I know it is a slightly different matter with the interior though:
I am also aware that the thread is not only much too coarse for scale, and that it extends all the way down to the bottom of the chamber, but I do take comfort in that still being quite a small object, it will be much easier to open, and then find the thread again when closing!
When I have finally established the precise nature of the internal feed tube, the majority of the chamber will be filled with a set, semi opaque solution to mimic a near full pot of steam oil, so hopefully by then the compromise won't be too obvious?!
I was so much enjoying the process that I quite forgot to photograph some of the sequences, so took some more - and still missed the critical bits! I append them here anyway:
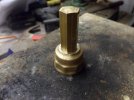
Once the hex is soldered into the factory machined bore, it provides a perfectly centred tail that can then be gripped firmly in both the bench vice and the drill chuck, without any fear of damaging the hollow shell. I did find it easier to remove the peaks off the octagonal grip section of the casting while still on the bench, and definitely before attempting to apply a hand held file to that part of the object when it is spinning in the drill.
There is still a bit of grooving to polish off, and working out the best method of shaping up their little conical, bobble hats from the blanking caps.
I do so like the idea of "upcycling" less obvious items for a new purpose, and while admittedly these were not found, second-hand donations or scrap, at least I now have a pair of these quirky little pots, plus some extra, vital bits of metal for less than a tenner of outlay!
Pete.
(The jammy bodger!)