GER open wagons
Liver & Fry
Western Thunderer
Apologies for any offence cause, but for me personally, I hate leaving a project unfinished. Generally when I start something, I like to get it done before I move on. However, because I'm still unsure about the wisdom of soldering with a wrist in cast, I've put the M&GN wagons on hold and my need to keep busy has pushed me in another direction.
@Herb Garden has previously dabbled with (what I hope he won't mind me calling) an experimental form of kit design, whereby a wagon should be made from the corresponding materials of a prototype; wood bodies being made of wood and metalwork being made of metal. Me and him are originally cut from the same GER cloth and so when he decided to use this method to design a kit/parts for some GER open wagons, how could I say no? Especially when it's a concept I fully endorse!
What I ended up with was some laser cut wood and a sheet of brass etch. My focus currently is on the wooden body so, here's what I had to work with:
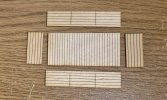
These parts will specifically make a Dia.17 open, of which 12,050 were built between 1886 and 1903 - Basically, if you model the GE, you need this wagon!
I also have some 7 plank sides which will allow construction of either a Dia.48 or a Dia.17R should I desire.
I started by fixing the ends to the floor using PVA:
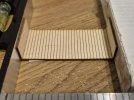
You may note I've slide a section of plasticard under the floor. This is to bring the floor to the correct height in relation to the half-plank at the bottom of the bodyside.
Next I affixed the sides:
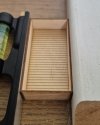
And once dry, I then cut a section of plasticard to the correct size and fitted it under the wooden floor:
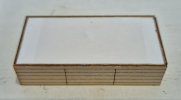
This has two benefits; the first is that the bottom of the wagon needs to be a flush surface to allow continuation of the kit built (raising the floor was me being unnecessarily pedantic) and the second is that this way provides additional floor strength.
So currently I now have a structurally rigid body for my wagon:
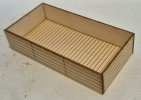
The nature of laser cut wood at this thickness means that only one side can be given planking, so my next move will be to add my own, in a similar manner to how I did the floor planking on the GE lowmac back at the start of my workbench thread. Yes, that steps away from "wood made from wood" but the final product will still, I'm sure, be something of great interest!
I'd just like to thank George for letting me have a go with these - I wouldn't have (and didnt) tackle these previously but now I feel like I can and I'm quite excited for the challenge of a different medium to work with.
As with the M&GN wagons, this may be a stop-start project depending on how I feel when I get to the metalwork section, but at least I've started it and done something!
- James
@Herb Garden has previously dabbled with (what I hope he won't mind me calling) an experimental form of kit design, whereby a wagon should be made from the corresponding materials of a prototype; wood bodies being made of wood and metalwork being made of metal. Me and him are originally cut from the same GER cloth and so when he decided to use this method to design a kit/parts for some GER open wagons, how could I say no? Especially when it's a concept I fully endorse!
What I ended up with was some laser cut wood and a sheet of brass etch. My focus currently is on the wooden body so, here's what I had to work with:
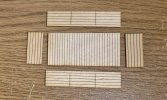
These parts will specifically make a Dia.17 open, of which 12,050 were built between 1886 and 1903 - Basically, if you model the GE, you need this wagon!
I also have some 7 plank sides which will allow construction of either a Dia.48 or a Dia.17R should I desire.
I started by fixing the ends to the floor using PVA:
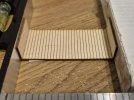
You may note I've slide a section of plasticard under the floor. This is to bring the floor to the correct height in relation to the half-plank at the bottom of the bodyside.
Next I affixed the sides:
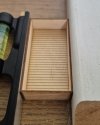
And once dry, I then cut a section of plasticard to the correct size and fitted it under the wooden floor:
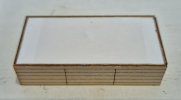
This has two benefits; the first is that the bottom of the wagon needs to be a flush surface to allow continuation of the kit built (raising the floor was me being unnecessarily pedantic) and the second is that this way provides additional floor strength.
So currently I now have a structurally rigid body for my wagon:
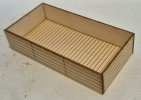
The nature of laser cut wood at this thickness means that only one side can be given planking, so my next move will be to add my own, in a similar manner to how I did the floor planking on the GE lowmac back at the start of my workbench thread. Yes, that steps away from "wood made from wood" but the final product will still, I'm sure, be something of great interest!
I'd just like to thank George for letting me have a go with these - I wouldn't have (and didnt) tackle these previously but now I feel like I can and I'm quite excited for the challenge of a different medium to work with.
As with the M&GN wagons, this may be a stop-start project depending on how I feel when I get to the metalwork section, but at least I've started it and done something!
- James
Last edited: