Right, slowly acquiring the required tools to get started, or replacing old knackered ones with new and better quality ones, today my SOBA machine vice turned up and very nice it is too, thanks to Steph for his mini review late last year which persuaded me to jump for one after
hand wringing eyeing them up for some time
Second is a home made drill table, I'd looked at Metalsmiths and thought I can make one of them, had to really as theirs is out of stock and no date for a new production run. So in my usual dock over engineering way I wandered down to the trailer shop to see if there were any steel plate off cuts, the polite chaps asked "waddya want mate" to whit I replied "steel plate, flatish and about yay big" gesticulating with ones hands, "what's it for" with a sideways glance, "home job mate" to which he broke into a grin and disappeared to return in swift fashion with said lump of steel.
Now I'd had in my mind to replicate Metalsmiths affair, but this lump of steel was significantly larger, it was after all part of a trailer rave (lump of steel at the corner of the trailer to stop 60T sliding off) and it's bleedin heavy, perfect I grinned, that's not going to go anywhere I thought.
So with said steel in ones hands....plural... I wandered next door to the turners shop and asked if I could 'borrow' some machine tools, "whats it for!", "home job mate", "ahh help yourself". So I did, 40mins on the 40" band saw found the sides squared off...as square as I need them....and another hour on the 24" swing lathe found me in the possession of a beautiful clean and flat piece of steel, trimmed up it weights in just a touch over 10Kg.
The only down side was the lathe cross feed auto speed was knackered and company cut backs have seen it not repaired, the auto cross feed works but only at the set speed, when turning large faces you need high speed, problem is the nearer you get to the centre the relative speed of the work decreases and so your finish suffers and the tool starts to rip the material. The auto cross feed speed works by speeding up the lathe the nearer the centre it gets, starting at the outside of the work at about 200rpm and should end up at the centre at maybe 1800rpm to retain the surface finish.
Sadly this has resulted in the outside of the flat faces being almost mirror finish but nearer the centre it's started to tear the surface so the whole lot will need dressing with ever finer abrasive papers in the power sander, in reality it's perfectly usable but looks a dogs dinner...to me anyway.
Final task was to drill and tap some 6mm holes for the clamps, haven't decided how many holes to drill so left it as the five shown here for the time being.
Why do I need a drill table, simples, I have four Stanier tender sides to bend along the cant rail and for all my back room bodgings I cannot tolerate in any slightest form curved areas that are not uniform in radius or have any sort of kink (of course now I'm going to be at home to Capt cock up on at least one bend). Cant rail curves are the most obvious in your face radius you see on a model so if you mess that up....it's going to show, hence the inordinate effort to make a drill table, procure correct radius stainless steel rod and clamps (need two more) before I even open the kit box, oh and the dozen or more practice attempts, luckily we use shim brass for motor alignment and there's plenty of off cuts lying around in motor rooms from previous shimming and motor replacements

, so the odd bit makes a run for. In short I can practice bending brass until I fall asleep LOL.
The Stanier tender bend is around 4" long so that's quite a length to get a uniform radius....for me anyway....and no, broom handles never did work very well for me, except, as broom handles, but never as brass former material LOL.
Next step is to machine up some flat bar so that I can bend square edges, the bar shown here is Aluminium and would probably do for small stuff like lamp irons, actually a steel rule would work better as it's thinner and easier to handle and see your work, but a nice steel sharp edged bar would be nice to add to the table.
So, getting closer to the doing stage, slowly slowly catchy monkey as we say around here

, granted you probably don't need any of these tools, but I like em and I enjoyed making the drill table. Just now waiting for the tool order from Squires to be ready to cut from etch and dress ready for bending and soldering
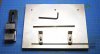