Tim Watson
Western Thunderer
The gear head for the Raven NER 4-6-2 has been made from a 6x10x10mm block of brass. This was initially an interference fit between the frames to help determine the worm and worm-wheel mesh.
The frames and block were then drilled for 14BA to hold this position.
The gap next to the opposite frame is just visible behind the shaft. The wheels are not at the final back to back measurement; allowing easy adjustment at this stage. The worm is twice as long as it needs to be and will be trimmed and a thrust washer placed next to the bearing.
The non-bolted side was trimmed back on some sharp Vallorbe files to be clear of the opposite frame (for electrical isolation).
The edges of the block were lightly bevelled - it’s engineering, not clockmaking where the edges should be sharp enough to cut…
Tim

The frames and block were then drilled for 14BA to hold this position.
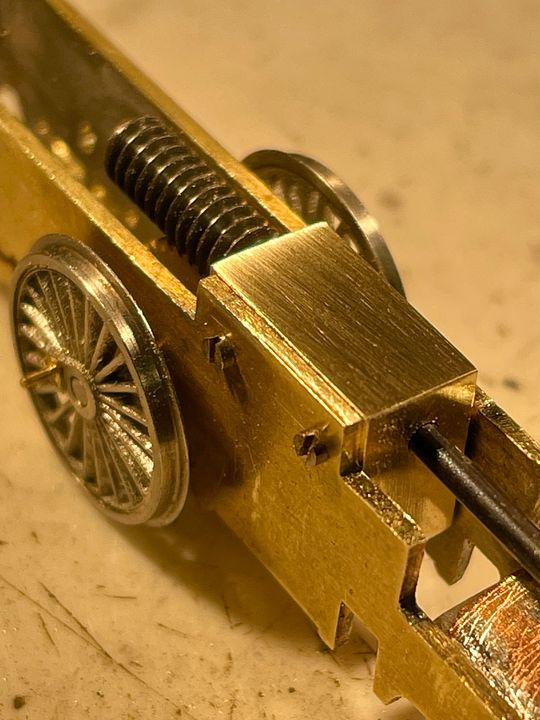
The gap next to the opposite frame is just visible behind the shaft. The wheels are not at the final back to back measurement; allowing easy adjustment at this stage. The worm is twice as long as it needs to be and will be trimmed and a thrust washer placed next to the bearing.
The non-bolted side was trimmed back on some sharp Vallorbe files to be clear of the opposite frame (for electrical isolation).
Tim