Still beavering away at the chassis. I had it running with just the inside motion for test today. Actually I had it running last night but then I realised that I had one of the insulated wheels on the wrong side so had to strip the rods off to swap it around.
As an aside I have reversed the front crankpin bushes to look more like the prototype and to give additional clearance for the motion. I was wondering about how to tighten the reversed bushes and remembered the late David Smith talking about making peg spanners as he called them. I chose a similar route but instead of pegs I used the same approach as the 4mm scale Romford screwdriver (I still have one in my modelling toolbox).
For those who haven’t a clue what I am talking about this is a Romford screwdriver
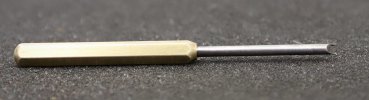
Original Romford Screwdriver
This is the leading crankpin bush that I am talking about
Front crank pin nut
This is the custom big boy’s ‘Romford’ Screwdriver that I made to tighten them. The business end is 3/16 silver steel and the end was shaped with a 3mm end mill with the rod held in a square collet block so that I could keep flipping it over to take the same amount off each side.
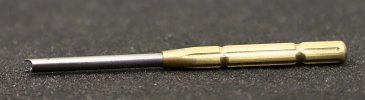
8BA Romford Screwdriver
Continuing my current ‘Dremel’ tool theme I used a ball burr in the mill to make the grip.
Previously I have used the ball burr in a similar manner to an end mill by cutting into the top of the work piece. This time I did it differently and side milled it. This gave a much better finish and was easier to do. I milled the grooves before turning the taper.