simond
Western Thunderer
I can see merits in both suggestions, though I’m at a loss to understand why not-very-hot steam should be any more deleterious to the bourdon tube than very-hot water.
I wonder if ensuring that the tube was full of water made it a bit heavier, thus reduced any tendency to vibrate? It would still vibrate, I guess, just more slowly, which might be preferable.
however I found this, which reiterates the point about temperature
blog.ashcroft.com
I wonder if ensuring that the tube was full of water made it a bit heavier, thus reduced any tendency to vibrate? It would still vibrate, I guess, just more slowly, which might be preferable.
however I found this, which reiterates the point about temperature
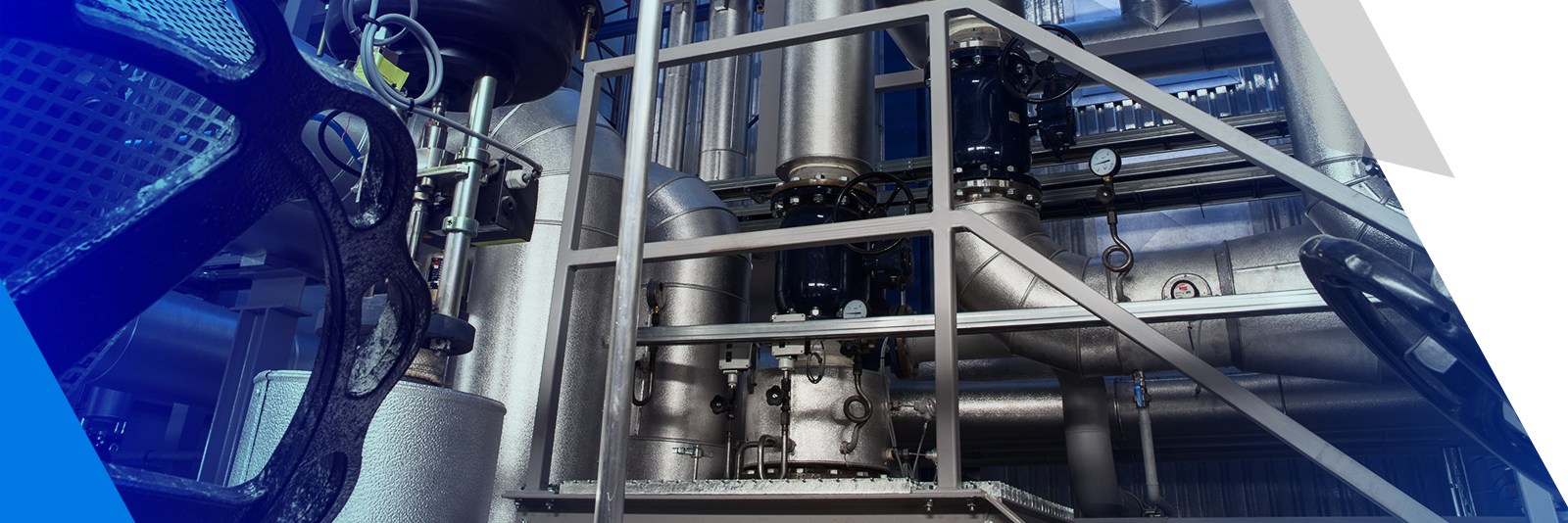
Why Do I Need a Steam Siphon and How Does It Work?
A steam siphon can be a very useful device. If you’re wondering how it works, this article will teach you.
